Cellulose Ether, Sodium Carboxymethyl Cellulose
Adhesion Effect
The adhesion of CMC in the slurry is attributed to the formation of a firm network structure through hydrogen bonds and van der Waals forces between macromolecules. When water penetrates into the CMC block, the hydrophilic groups with less water attraction swell, while the more hydrophilic ones separate immediately after swelling. The inhomogeneous hydrophilic groups in CMC production result in inconsistent dispersed particle size of micelles. Hydration swelling occurs inside the micelles, forming a bound water layer outside. In the early stage of dissolution, the micelles are free in the colloid. The van der Waals force gradually brings the micelles together, and the bound water layer forms a network structure due to the asymmetry of size and shape. The fibrous CMC network structure has a large volume, strong adhesion, and reduces glaze defects.
levitation Effect
Without additives, glaze slurry will settle due to gravity over time, and adding a certain amount of clay is not sufficient to prevent this from happening. However, the addition of a certain amount of CMC can form a network structure that supports the gravity of the glaze molecules. The CMC molecules or ions stretch in the glaze and occupy space, preventing the mutual contact of glaze molecules and particles, which improves the dimensional stability of the slurry. In particular, the negatively charged CMC anions repel the negatively charged clay particles, leading to increased suspension of the glaze slurry. This means that CMC has good suspension in the glaze slurry. The network structure formed by CMC also helps to reduce glaze defects and ensure a smooth surface finish. Overall, CMC plays a crucial role in the stability and suspension of glaze slurry, which is important for achieving consistent and high-quality results in the glazing process.
Questions to Consider when Choosing a CMC
The proper use of CMC in the production of glaze can greatly improve the quality of the final product. To ensure the best effect, there are several key points to follow. Firstly, it is important to check the CMC model specification before purchasing and choose a suitable specification for production. When adding CMC to the glaze during milling, it can help to improve milling efficiency. Attention should also be paid to the water-to-CMC ratio when pouring water to achieve the maximum effect.
The glaze slurry should be allowed to rot for a day or two to ensure it is stable enough and the CMC can play the best effect. It is also important to properly adjust the amount of CMC added according to seasonal changes, with the most added in summer, the least in winter, and a range of 0.05% to 0.1% in between. If the dosage is left unchanged in winter, it can cause runny glaze, slow drying, and sticky glaze. Conversely, insufficient dosage will result in a dense and rough glaze surface.
In summer, high temperatures can degrade the viscosity of CMC due to bacterial influence. Therefore, it is necessary to perform anti-corrosion work and add suitable additives to maintain CMC quality. Finally, when using the glaze, it is recommended to sieve it with a sieve above 100 mesh to prevent the residue of CMC from affecting the glaze surface during firing. By following these guidelines, CMC can be used effectively in glaze production to improve product quality.
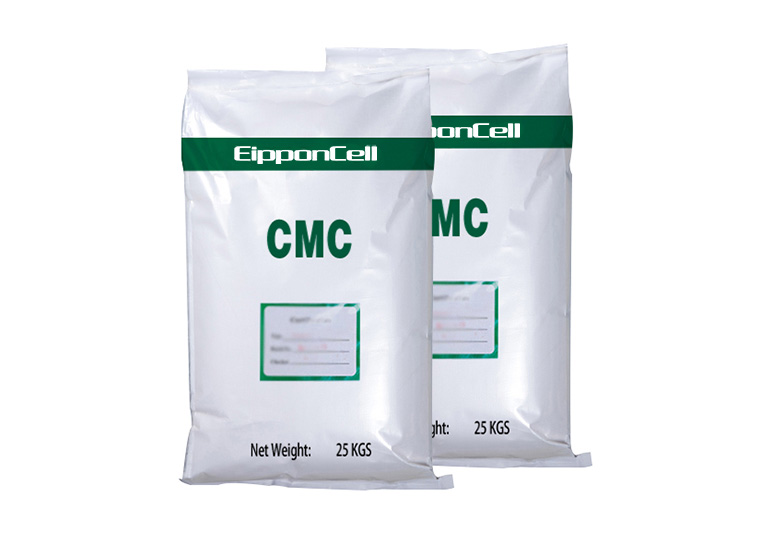